DGS Control & Monitoring System
DGS CONTROL SYSTEM
The Dry Gas Seal Control System is designed to provide the following features:
- Filter the process gas and supply clean gas to the primary seal
- Regulate the differential pressure of seal gas.
- Monitor seal performance and
- Provide Alarm/ shut down signals.
Gas from either compressor’s discharge or from an alternate source passes through the filters, to be regulated at pressure slightly higher than the compressor suction/ balance line pressure. This clean & dry gas is then directed to the seals.
Since the seals mating rings rotate with shaft, small amount of gas are pumped inward between the faces. A sealing dam restricts gas flow providing a pressure rise in the outer portion of the faces. This creates a small gap between the faces that keeps them separated to prevent any wear. A small amount of gas pass through the faces and is directed to the control panel where instruments monitor seal performance and provide measurements about the seals operation based on this leakage flow and pressure.
Appropriate action should be taken in regards to the control panel measurements to maintain the equipment’s safe operation.
Notes:
- Regulated Seal Barrier Gas Pressure should be maintained 0.3/0.5 bar higher than the compressor suction / balance line pressure. This can be controlled with the help of differential pressure control valve arrangement installed in the filter skid.
- Variation to this value (higher or lower) depends upon the stability of such pressure and will vary from installation to installation.
- To maintain constant barrier gas flow to the seals, one filter is operating while the other one is in standby.
- The most important component in the control panel system is the filter and Differential pressure control valve. The ability to maintain a supply of clean, dry gas will provide the best probability of long seal life.
The control panel designed to control & monitor of dry gas seals installed in both Drive end & Non drive end side of the compressor.
Seal Gas Control Methods
The flow of seal gas to a primary seal is controlled by either a flow control method or a differential pressure control method. The main objective of both types of control methods is to positively sweep the seal gas across the process gas labyrinth to prevent a reverse flow of process gas into the dry gas seal.
A flow-control system controls the supply of seal gas to the seals by regulating the seal gas flow through an orifice upstream of each seal. It includes a valve with a remote flow controller that compares the seal gas flow to each seal and adjusts the flow control valve to maintain a minimum 16 fps (4.9 m/s) flow velocity across the inner process labyrinth seal based on “high select reference pressure” for each seal, measured downstream of the flow orifices.
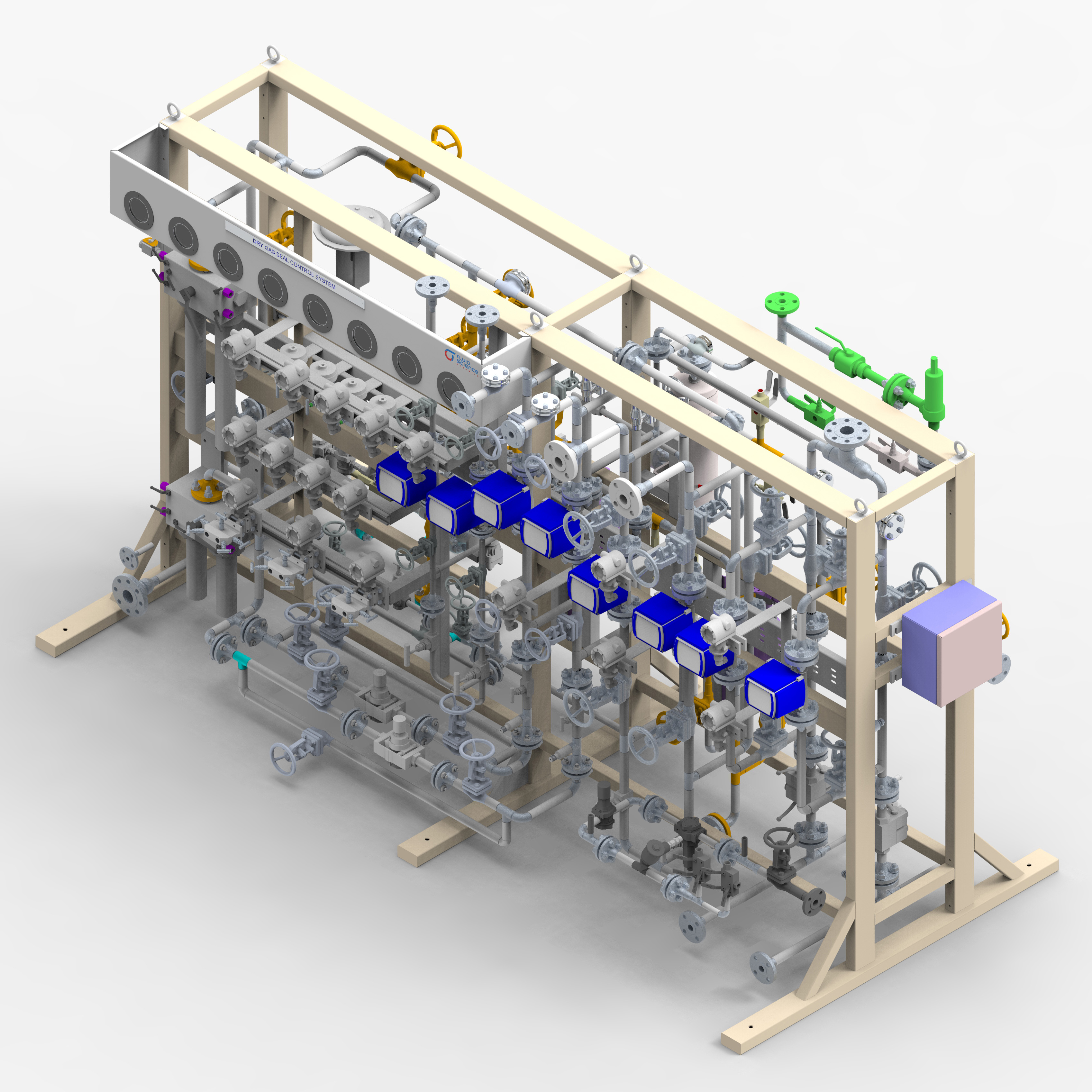